Development Report:
Low-Cost Design Solutions for Educational Robots
Monica Tiboni*, Francesco Aggogeri*, Roberto Bussola*, Alberto Borboni*, Cesare Augusto Perani**, and Nicola Pellegrini*
*Università degli Studi di Brescia
Via Branze 38, Brescia 25123, Italy
**XPLAB
Viale S. Eufemia 39, Brescia 25139, Italy
Low-cost robotics, fully integrated in the corporate IT infrastructure, is a requirement in the era of modern industrial automation derived from the Industry 4.0 model. This paper presents a multidisciplinary robotics-based learning (R-BL) project consisting of the development of a modular control architecture and a gripper for small manipulators. The solution, as compared with options available in the current robotic market, is a balance between low-cost devices with industrial robot performance. The project is carried out as part of the Robotics and Mechanisms program, a course in the automation engineering degree program at the University of Brescia in Italy. A 4-axis small-size robot, able to manipulate many kinds of objects, was designed and built by a student team by integrating the controller and the gripper. The controller was implemented using a real-time Raspberry platform by following a modular design concept. The control software is characterized by a short development time. The gripper was advanced to achieve low cost and modularity tradeoffs.
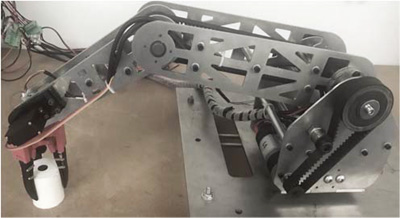
Picture of robotic manipulator
- [1] Z. M. Bi and W. J. Zhang, “Modularity Technology in Manufacturing: Taxonomy and Issues,” Int. J. Adv. Manuf. Technology, Vol.18, pp. 381-390, 2001.
- [2] B. Gombert, G. Hirzinger, G. Plank, and M. Schedl, “Modular concepts for a new generation of light weight robots,” Industrial Electronics, Control & Instrumentation, Vol.3, pp. 1507-1514, 1994.
- [3] R. Kolluru, K. P. Valavanis, N. Tsourveloudis, and S. Smith, “Design Fundamentals of a Reconfigurable Robotic Gripper System,” IEEE Trans. on System, Man and Cybernetics, Vol.30, No.2, Part A, pp. 181-187, 2000.
- [4] S. Cinquemani, H. Giberti, and G. Legnani, “Kinematic Optimization of a 2DoF PRRRP Manipulator,” Advances in Italian Mechanism Science, Mechanisms and Machine Science, Vol.47, Springer, 2017.
- [5] M. Serpelloni, M. Tiboni, M. Lancini, S. Pasinetti, A. Vertuan, and M. Gobbo, “Preliminary study of a robotic rehabilitation system driven by EMG for hand mirroring,” Proc. of IEEE Int. Symp. on Medical Measurements and Applications, MeMeA 2016, No.7533730, 2016.
- [6] H. Giberti, E. Fiore, and A. Saccomani, “On the Mechatronic Design of a Low-Cost 6-DoFs Parallel Kinematic Manipulator,” Mechanisms and Machine Science, Vol.49, pp. 46-54, 2018.
- [7] E. Uhlmann, F. Elbing, and J. Dittberner, “Innovative manufacturing technologies for the disassembly of consumer goods,” J. of Engineering Manufacture, Vol.218, No.9, pp. 1039-1046, 2004.
- [8] M. Tiboni, G. Legnani, M. Lancini, M. Serpelloni, M. Gobbo, and D. Fausti, “ERRSE: Elbow robotic rehabilitation system with an EMG-based force control,” Mechanisms and Machine Science, Vol.49, pp. 892-900, 2018.
- [9] S. Popic and B. Miloradović, “Light weight robot arms – an overview,” Proc. of Infoteh, pp. 818-822, 2015.
- [10] J. Angeles, “Fundamentals of Robotic Mechanical Systems: Theory, Methods and Algorithms,” Springer-Verlag, 1997.
- [11] O. Ibrahim and W. Khalil, “Kinematic and dynamic modeling of the 3-RPS parallel manipulator,” Proc. of the 12th IFToMM World Congress, 2007.
- [12] Y. Qin, K. Zhang, J. Li, and J. S. Dai, “Modelling and analysis of a rigid-compliant parallel mechanism,” Robot. Comput.-Integr. Manuf., Vol.29, pp. 33-40, 2013.
- [13] F. Aggogeri, N. Pellegrini, and R. Adamini, “Functional Design in Rehabilitation: Modular Mechanisms for Ankle Complex,” Applied Bionics and Biomechanics, Vol.2016, Art. 9707801, 2016.
- [14] E. Fiore, H. Giberti, and G. Bonomi, “An innovative method for sizing actuating systems of manipulators with generic tasks,” Mechanisms and Machine Science, Vol.47, pp. 297-305, 2017.
- [15] S. Jung, “Experiences in developing an experimental robotics course program for undergraduate education,” IEEE Trans. Educ., Vol.56, No.1, pp. 129-136, 2013.
- [16] C.-S. Lee, J.-H. Su, K.-E. Lin, J.-H. Chang, and G.-H. Lin, “A project-based laboratory for learning embedded system design with industry support,” IEEE Trans. Educ., Vol.53, No.2, pp. 173-181, 2010.
- [17] S. E. Kerns, R. K. Miller, D. V. Kerns, and National Academy of Sciences, “Designing from a blank slate: The development of the initial olin college curriculum,” Educating the Engineer of 2020: Adapting Engineering Education to the New Century, Nat. Acad. Press, pp. 105-113, 2005.
- [18] N. K. Uttarkar and R. R. Kanchi, “Design and development of a lowcost embedded system laboratory using TI MSP430F149,” Proc. Int. Conf. Commun. Signal Process. (ICCSP), pp. 165-175, 2013.
- [19] S. Ahmad, “A laboratory experiment to teach some concepts on sensor-based robot assembly systems,” IEEE Trans. Educ., Vol.31, No.2, pp. 74-84, 1988.
- [20] R. H. Chu, D. D. C. Lu, and S. Sathiakumar, “Project-based lab teaching for power electronics and drives,” IEEE Trans. Educ., Vol.51, No.1, pp. 108-113, 2008.
- [21] W. Durfee, P. Li, and D. Waletzko, “Take-home lab kits for system dynamics and controls courses,” Proc. Amer. Control Conf., Vol.2, pp. 1319-1322, 2004.
- [22] M. Gunasekaran and R. Potluri, “Low-cost undergraduate control systems experiments using microcontroller-based control of a DC motor,” IEEE Trans. Educ., Vol.55, No.4, pp. 508-516, 2012.
- [23] J. Rodriguez-Resendiz, G. Herrera-Ruiz, and E. A. Rivas-Araiza, “Adjustable speed drive project for teaching a servo systems course laboratory,” IEEE Trans. Educ., Vol.54, No.4, pp. 657-666, 2011.
- [24] M. Hedley and S. Barrie, “An undergraduate microcontroller systems laboratory,” IEEE Trans. Educ., Vol.41, No.4, p. 345, 1998.
- [25] A. Kommu, R. R. Kanchi, and R. P. G. Varadarajula, “Design and development of a low-cost student experiments for teaching ARM based embedded system laboratory,” Proc. IEEE Int. Conf. Teach. Assessment Learn. Eng. (TALE), pp. 515-520, 2013.
- [26] C. Parikh, “Autonomous robot: An intellectual way of infusing microcontroller fundamentals into sophomore students,” Proc. IEEE Frontiers Educ. Conf., pp. 1-4, 2015.
- [27] J. Solis, R. Nakadate, T. Yamamoto, and A. Takanishi, “Introduction of mechatronics to undergraduate students based on robotic platforms for education purposes,” Proc. 18th IEEE Int. Symp. Robot Human Interact. Commun., pp. 693-698, 2009.
- [28] R. Grover, S. Krishnan, T. Shoup, and M. Khanbaghi, “A competition-based approach for undergraduate mechatronics education using the arduino platform,” Proc. 4th Interdiscipl. Eng. Design Educ. Conf., pp. 78-83, 2014.
- [29] J. Froyd and National Academy of Sciences, “The engineering education coalitions program,” Educating the Engineer of 2020: Adapting Engineering Education to the New Century, Nat. Acad. Press, pp. 81-93, 2005.
- [30] B. T. Chowdhury, S. M. Kusano, A. Johri, and A. Sharma, “Student experiences in an interdisciplinary studio-based design course: The role of peer scaffolding,” Proc. 121st ASEE Annu. Conf. Expo., pp. 1-13, 2014.
- [31] K. Jablokow, J. V. Matson, and D. Velegol, “A multidisciplinary MOOC on creativity, innovation, and change: Encouraging experimentation and experiential learning on a grand scale,” Proc. 121st ASEE Annu. Conf. Expo., pp. 1-23, 2014.
- [32] J. A. Piepmeier, B. E. Bishop, and K. A. Knowles, “Modern robotics engineering instruction,” IEEE Robot. Autom. Mag., Vol.10, No.2, p. 3337, 2003.
- [33] K. Nagai, “Learning while doing: Practical robotics education,” IEEE Robot. Autom. Mag., Vol.8, No.2, p. 3943, 2001.
- [34] E. Krotkov, “Robotics laboratory exercises,” IEEE Trans. Educ., Vol.39, No.1, p. 9497, 1996.
- [35] M. F. Robinette and R. Manseur, “ROBOT-DRAW, an internet-based visualization tool for robotics education,” IEEE Trans. Educ., Vol.44, No.1, p. 2934, 2001.
- [36] M. Hernando, R. Galan, I. Navarro, and D. Rodriguez-Losada, “Ten years of Cybertech: The educational benefits of bullfighting robotics,” IEEE Trans. Educ., Vol.54, No.4, pp. 569-575, 2011.
- [37] H. Hassan, J. M. Martinez, C. Dominguez, A. Perles, and J. Albaladejo, “Innovative methodology to improve the quality of electronic engineering formation through teaching industrial computer engineering,” IEEE Trans. Educ., Vol.47, No.4, pp. 446-452, 2004.
- [38] G. Solomon, “Project-based learning: A primer,” Technol. Learning, Vol.23, pp. 20-30, 2003.
- [39] M. Somerville et al., “The Olin curriculum: Thinking toward the future,” IEEE Trans. Educ., Vol.48, No.1, pp. 198-205, 2005.
- [40] R. Murphy, “’Competing’ for a robotics education,” IEEE Robot. Autom. Mag., Vol.8, No.2, pp. 44-55, 2001.
- [41] C. Kitts, “Surf, turf, and above the Earth,” IEEE Robot. Autom. Mag., Vol.10, No.3, pp. 30-36, 2003.
- [42] J. R. Savery and T. M. Duffy, “Problem based learning: An instructional model and its constructivist framework,” Educ. Technol., Vol.35, No.5, pp. 31-38, 1996.
- [43] J. Solis and A. Takanishi, “Practical issues on robotic education and challenges towards roboethics education,” Proc. 18th IEEE Int. Symp. Robot Human Interactive Commun., pp. 561-565, 2009.
- [44] J. Macias-Guarasa, J. M. Montero, R. San-Segundo, A. Araujo, and O. Nieto, “A project-based learning approach to design electronic systems curricula,” IEEE Trans. Educ., Vol.49, No.3, pp. 389-397, 2006.
- [45] W. Daems et al., “PeopleMover: An example of interdisciplinary project-based education in electrical engineering,” IEEE Trans. Educ., Vol.46, No.1, pp. 157-167, 2003.
- [46] S. Jung, “Experiences in Developing an Experimental Robotics Course Program for Undergraduate Education,” IEEE Trans. Educ., Vol.56, No.1, pp. 129-136, 2013.
- [47] M. Ceccarelli, “Robotic teachers assistants,” IEEE Robot. Autom. Mag., Vol.10, No.3, p. 3745, 2003.
- [48] A. Leopoldo, “Low-cost Printable Robots in Education, Fuentes-Dur Pedro, Perry David,” J. of Intelligent and Robotic Systems, Vol.81, p. 1, 2016.
- [49] Z. Lu, A. Chauhan, F. Silva, and L. S. Lopes, “A brief survey of commercial robotic arms for research on manipulation,” Proc. IEEE Symp. Robot. Appl., pp. 986-991, 2012.
- [50] I. Ebert-Uphoff, “Introducing parallel manipulators through laboratory experiments,” IEEE Robotics & Automation Magazine, Vol.10, No.3, p. 9, 2003.
- [51] K. Takahashi, M. D. Best, N. Huh, K. A. Brown, A. A. Tobaa, and N. G. Hatsopoulos, “Encoding of Both Reaching and Grasping Kinematics in Dorsal and Ventral Premotor Cortices,” J. Neurosci., Vol.37, No.7, pp. 1733-1746, 2017.
- [52] L. Zhou, S. Bai, and M. R. Hansen, “Integrated dimensional and drive-train design optimization of a light-weight anthropomorphic arm,” Robotics and Autonomous Systems, Vol.60, Issue 1, pp. 113-122, 2012.
- [53] C. A. Perani, “POWER-KI Preludio: a programming language,” XPLAB Research in Automation, 2012.
- [54] R. R. Ma, L. U. Odhner, and A. M. Dollar, “A modular, open-source 3d printed under actuated hand,” 2013 IEEE Int. Conf. on Robotics and Automation (ICRA), 2013.
- [55] A. Dollar and R. Howe, “A robust compliant grasper via shape deposition manufacturing,” IEEE/ASME Trans. on Mechatronics, Vol.11, No.2, pp. 154-161, 2006.
- [56] N. Pellegrini, “A thermo-dynamical constitutive model based on kinetic approach for shape memory materials,” Advances Materials Research, Vol.651, pp. 42-48, 2013.
- [57] A. Gegeckaite, H. N. Hansen, L. De Chiffre, and P. Pocius, “Handling of Micro Objects: Investigation of Mechanical Gripper Functional Surfaces,” Proc. of 7th EUSPEN Int. Conf., pp. 185-188, 2007.
- [58] S. Ruggeri, G. Fontana, G. Legnani, and I. Fassi, “Design Strategies for Vacuum Micro-Grippers With Integrated Release System,” 11th Int. Conf. on Micro- and Nanosystems, 2017.
- [59] G. J. Monkman, S. Hesse, R. Steinmann, and H. Schunk, “Robot Grippers,” WILEY-VCH Verlag GmbH & Co. KGaA, 2007.
- [60] G. Fantoni, J. Tilli, and S. Capiferri, “Method for supporting the selection of robot grippers,” The CIRP 24th Design Conf., 2014.
- [61] L. Natale, F. Orabona, G. Metta, and G. Sandini, “Exploring the world through grasping: a developmental approach,” Proc. 2005 IEEE Int. Symp. on Computational Intelligence in Robotics and Automation, pp. 559-565, 2005.
- [62] A. Bicchi and V. Kumar, “Robotic grasping and contact: a review,” Proc. 2000 ICRA. Millennium Conf. IEEE Int. Conf. on Robotics and Automation, Vol.1, pp. 348-353, 2000.
- [63] K. Hsiao, P. Nangeroni, M. Huber, A. Saxena, and A. Y. Ng, “Reactive grasping using optical proximity sensors,” Proc. 2009 ICRA. IEEE Int. Conf. on Robotics and Automation, pp. 2098-2105, 2009.
- [64] G. Bone, A. Lambert, and M. Edwards, “Automated modeling and robotic grasping of unknown three-dimensional objects,” 2008 IEEE Int. Conf. on Robotics and Automation, pp. 292-298, 2008.
This article is published under a Creative Commons Attribution-NoDerivatives 4.0 Internationa License.